
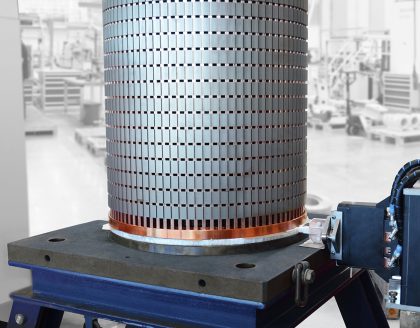
A face heating coil is shown here brazing a squirrel cage rotor for a wind turbine.
Induction heating coils are used to precisely and efficiently braze joints, assemble and disassemble metal parts, harden dies, anneal metal surfaces for additional flexibility and strength and more. Used in combination with a generator designed with the correct frequency and power for the job as well as with an optimized manufacturing process, inductors can improve the quality of joints, speed up production time and reduce your energy costs.
Table of Contents:
- Inductor coil manufacturing to optimize your equipment performance
- Flexible coil production and service options
- Custom manufactured inductors for a range of applications
- Types of induction coils and uses
- Induction heating coil prices
- The leading induction heating coil manufacturer serving US, Canada & Mexico
Inductor coil manufacturing to optimize your equipment performance
Improving part quality and the speed and efficiency of your manufacturing processes requires topnotch inductors as well as first-class power supplies. Temperature accuracy plays a critical role, and precise heating is only possible with the right mix of inductor geometry, frequency, power and magnetic field properties. This requirement calls for specialized expertise in inductor manufacturing.
For more than 22 years, eldec LLC has custom manufactured induction heating coils in Auburn Hills, Michigan. Our technicians have a thorough understanding of induction heating applications. They know results depend on the type and quality of inductor used. The shape of the tool must be customized very precisely to match the part. For this reason, eldec believes every quote should begin with a review of part drawings or actual parts with the customer to fine tune the production process in order to improve an inductor’s precision and efficiency.
Flexible coil production and service options
Once the review process is complete, our technicians design the inductor with the aid of the latest 3D CAD software, physically test the final coil design on the real part and develop a recipe (power and time settings) for the final production process.
Another important aspect of eldec’s services is the high degree of flexibility offered in inductor design and production. Customers requiring a certain number of the same tools each year can enter into a framework agreement with us. eldec then produces the new inductor on a just-in-time basis, minimizing lead times and stock quantities.
-
Custom inductor design and fabrication: induction coils engineered for your part and your process and built when you need them.
-
Inductor repair and maintenance: repairs can be performed no matter if eldec made them originally or if they were manufactured by one of our competitors.
-
Inductor manufacturing training: courses include theoretical principles and practical exercises.
-
Request a quote for induction coils
-
Use eldec’s Coil Design Assistant: an online app that allows you to select from commonly purchased basic coil designs and submit an RFQ without creating and uploading draft coil drawings.
The combination of specialized training for your staff, process development assistance from eldec’s knowledgeable technicians as well as eldec’s high quality inductors and power supplies can make a difference in your plant. Gains in efficiency can reduce the time needed from start to finish in producing your parts, please your customers, and also reduce your carbon footprint and utility costs.
Custom manufactured inductors for a range of applications
Whether your parts are large or small, simple or complex, eldec can manufacture inductors specifically for your workpiece, your process and your metal type.
-
Induction heating coils for induction brazing – create stronger and more precise joints
-
Induction heating coils for shrink fitting – make assembly and disassembly of metal components fast and simple
-
Induction heating coils for die hardening – keep dies sharper and stronger longer
-
Induction heating coils for induction annealing – help prevent stress fractures in critical parts
Manufacturing companies in the aerospace, automotive, electric motors, HVAC, mining, power generation, oil/gas production and distribution, agriculture and medical device sectors – to name a few – rely on eldec induction heating coils. New uses for induction technology are only limited by your imagination.
Types of induction coils and uses
An inductor’s shape and construction style are determined predominantly by the geometry of the workpiece section to be heated, and the possibilities are infinite. The following list is a guide to basic types of inductors and possible uses.
Fork Coils
Fork coils have two fork-like tines that are used to heat two opposing sides of a workpiece. They are often used for brazing applications. Types of fork coils include:
-
- Straight
-
- 90 Degree
-
- Flex Loop
-
- Offset
-
- Straight Miter
-
- 90 Degree Miter
Face Heating Coils
Face heating coils have a flat heating face on the head that heats a workpiece from only one side. This type of coil can be used for general warming and various brazing applications. Types of face heating coils include:
-
- Short Circuit Ring
-
- Pretzel
-
- Spiral
-
- Meander
Outside and Inside Heating Coils
Outside and Inside Heating Coils have one or more turns of tubing for a head and are commonly used for either in-field or out-field heating on workpieces, where the desired heat zone is limited in width or where the desired heat zone is larger in width than a single turn coil. Types include:
-
- Single Turn Outside
-
- Multi Turn Outside
-
- Rectangular Outside
Hairpin Coils
Hairpin Coils inductors are designed with a simple out-and-back heating face. They are used when the required heat band is narrow and only accessible from one side. Types include:
-
- Straight Hairpin
-
- 90 Degree Hairpin
-
- 90 Degree Hairpin
Flexible Heating Cable and Cable Box
Flexible Heating Cable and Cable Boxes are used when the workpiece is too large for a conventional inductor. The heating cable works similarly to an induction coil; however, the cable is wrapped around the workpiece. Heating cable pricing varies based on length. Standard length of 15 meters is roughly $3,000. The cable box itself would be part of the cost of a generator – similar to a coax.
If you’re not sure which type of coil will work best for your process, let eldec’s technicians review your process and help you decide which coils to use.
Induction heating coil prices
Since inductors vary in size and shape depending on the process, materials and parts, prices vary as well. Most induction heating coils range from $1,200 to $3,000 in US Dollars. For example, a small fork coil with no laminations or ceramic coating might cost closer to $1,000; whereas, a large face heating coil with a complex housing / support structure could be tens of thousands of dollars. All of our coils are custom made. None are considered off-the-shelf; however, eldec can manufacture coils that are commonly used at your plant to be delivered in a just-in-time basis, minimizing lead times and reducing the need for stock quantities.
The leading induction heating coil manufacturer serving US, Canada & Mexico
Our coils have been called the Cadillac of inductors by one of our customers. Paul George, induction brazing consultant for Outage Technology Solutions and former brazing instructor for GE Power Division, argues other companies may make cheaper coils, but eldec’s dedication to quality, technical support, reliable delivery dates and great working relationships place us second to none. We’re proud of our “date promised, date delivered” reputation and the fact that customers trust us to protect their proprietary information.
Your parts and manufacturing processes are unique. At eldec, every project begins with a design review and process development discussions. Our experienced team will help you chose an induction power supply and design induction coils for your specific parts and production environment. And, if induction heating is new to you and your staff, operator and maintenance training is available in our plant in Auburn Hills, Michigan or at your site. Schedule a consultation today to get the discussions started.